“Natural, eco-friendly, peerless. For more than 150 years we’ve been perfecting the traditional craft of vegetable tanning. A labor-intensive method, it produces superior leathers full of character. Here’s, a look at the process.”
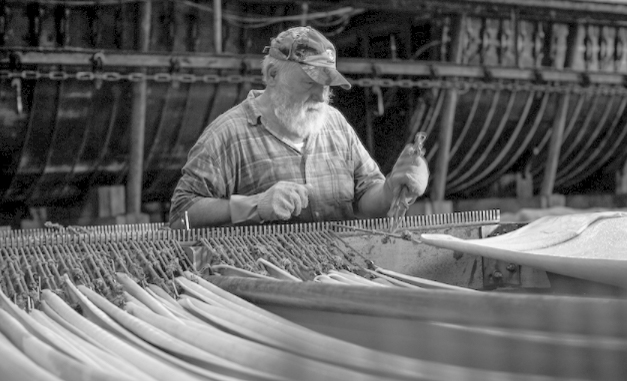
Understanding Taza’s moral obligation, knowing where our raw products are coming from and the process to produce these beautiful pieces is just the start. I will share from the get go the process our leather providers take as well as their morals. This company is 100% American, continuing the tradition of vegetable dying leathers. One of the last standing tanneries with these characteristics. I see leather as more than a fashion statement, but as a utilitarian tool, that passes through time with the least impact on the finances of the buyer and the footprint on the planet.
1). Pre-Tanning
Before the tanning process can commence, hides must be properly prepped. Sourced from North American cattle of European stock, we spend two days rehydrating and removing the hair. Excess flesh on the hide is removed on a Fleshing Machine and then each hide is cut into two sides.
2). Tanning
The split hides are moved to the tanning yard – a large space compromised of 72 vats, each one filled with a proprietary blend of natural tannins that include the bark of Mimosa and Quebracho trees. The hides spend two weeks soaking in this special tanning liquor, which we continually replenish and recirculate to guarantee deep, allover absorption. Once out of the yards, sammying removes excess moisture, a pre-grade is assigned and then the tanned hides are split to desired thickness and further shaved to even out thickness.
3). Dyeing, Fat Liquoring,
DryingTanned hides are like blank canvases and it is here, in this stage, where they are transformed into richly colored leathers. Different dyes of varying shades are applied through a process called drum dyeing. The hides are then fat-liquored with conditioning oils and waxes. English Bridle and Harness leathers are further hot stuffed, which literally means they’re stuffed to the core with nourishing waxes and tallows for an even deeper concentration of color and greater durability. Once dyed and nourished, the drying process begins. Following sammying, the leathers are set out to remove any wrinkles before toggle drying. Stretched out and clamped on a perforated stainless steel screen, the hides are air dried in a climate-controlled, dehumidified space for around three days before undergoing the final step: staking, which softens the hides.
4). Finishing
At this point, the tanned, dyed, conditioned and soften hides are almost ready for delivery. They’re sprayed one more time with a mix of special waxes for feel and protection, then with polyurethane for abrasion resistance. Finally, they’re ironed to render the surface smooth and even. A final grade is given and the leathers are shipped. The entire process takes around six weeks, which is exponentially more than the chrome tanning, but the results speak for themselves.
Leather working is a tradition and the products produced are utilitarian commodities. Moderation and mindfulness from the consumer is what will really leaves a lasting effect. An informed consumer with mindful respect will be necessary to achieve this.
2 thoughts on “Our Leather”
Enjoyed reading the content above, really explains everything in detai,,
the guide is extremely interesting and effective.
Best regards,
Dinesen Hessellund
Thank you Dinesen,